Abbattimento dei rischi di errore umano, massima visibilità del funzionamento degli impianti, ottimizzazione di produzione e gestione del magazzino, miglioramento della sicurezza fisica per il personale e di quella IT per impianti e dispositivi connessi. Se qualcuno si sta domandando quali possano essere concretamente i benefici di una rivoluzione dell’industria in chiave 4.0, negli stabilimenti di Ravenna e Casalmaggiore del gruppo Marcegaglia troverà probabilmente risposte interessanti.
Per un colosso mondiale della trasformazione di acciaio, che conta 43 stabilimenti per una superficie produttiva di 6 milioni di metri quadrati e che realizza ogni giorno 5.500 chilometri di manufatti, sposare la quarta rivoluzione industriale ha rappresentato fin dal principio una sfida tanto complessa quanto ambiziosa. Specialmente nelle grandi compagnie andare per gradi è più un obbligo che una scelta. E così è avvenuto per Marcegaglia che ha nel 2009 ha avviato un percorso di ampliamento degli spazi e rinnovamento tecnologico, investendo circa 250 milioni su due dei suoi impianti italiani e trovando in Cisco un partner fondamentale.
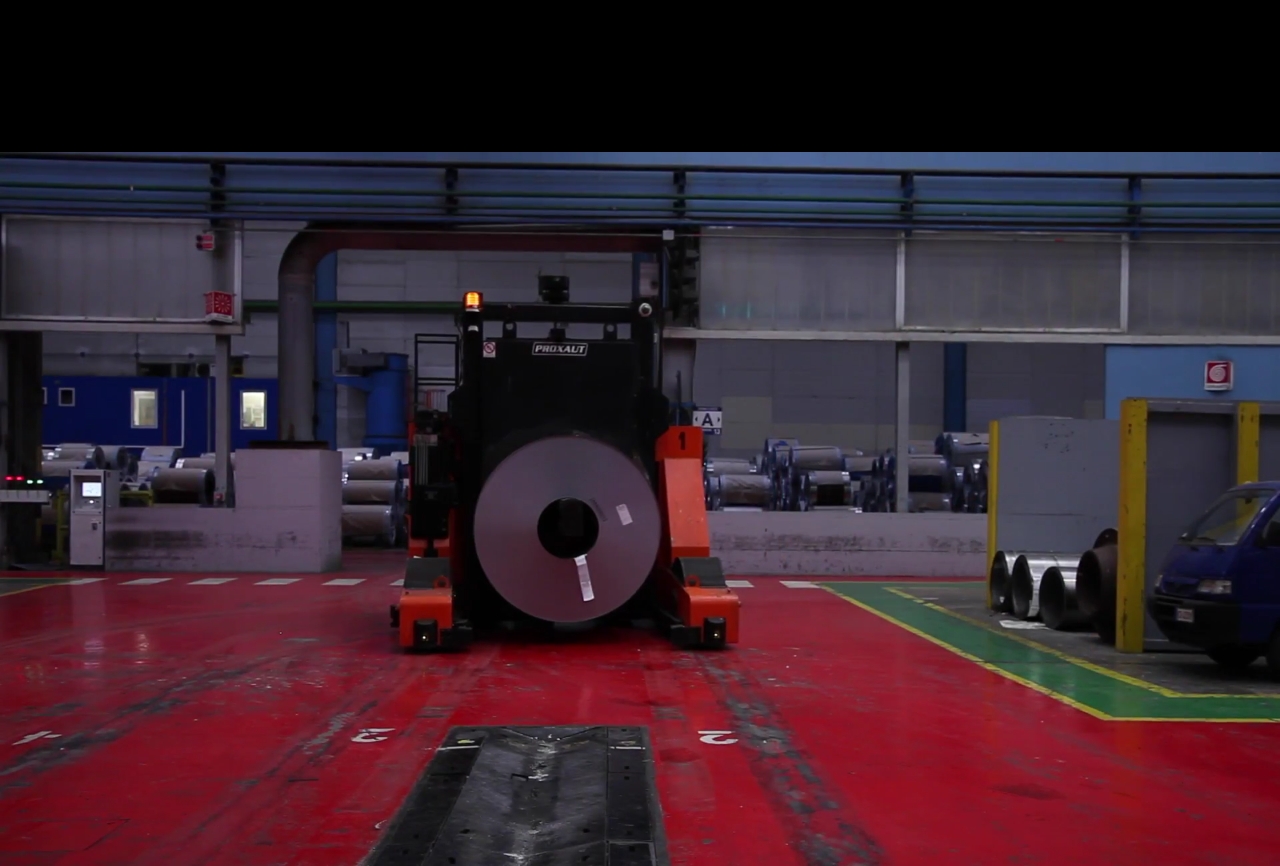
La sfida di Marcegaglia – Tre i pilastri del progetto di riconversione digitale degli impianti: allestire un’architettura di rete, cablata e wireless, in grado di assicurare l’efficienza degli impianti automatizzati; ottimizzare produttività e logistica attraverso sistemi automatici di stoccaggio prodotti finiti e movimentazione coils; garantire altissimi livelli di affidabilità e sicurezza negli stabilimenti. Per raggiungere questi obiettivi il duo Marcegaglia-Cisco ha deciso di corredare i nuovi impianti di produzione di sistemi automatizzati per tutte le operazioni di movimentazione della materia prima, nonché di spostamento e stoccaggio dei prodotti, lungo le varie fasi di lavorazione. Un processo di digital transformation che, avendo avuto bisogno di un’architettura di rete in grado di scambiare dati e informazioni con i nuovi impianti integrati negli stabilimenti, ha anche individuato nella cybersecurity un asse portante per far convivere uomo, macchina e acciaio.
Robot autonomi e stoccaggio hi-tech, sprint automazione – Essendo i due stabilimenti di Ravenna e Casalmaggiore dedicati ad attività differenti, altrettanto differenti sono i device e i sistemi attualmente installati. Nell’impianto emiliano, specializzato in trattamento e nobilitazione dei cosiddetti coils, ossia delle gigantesche bobine di acciaio, ha iniziato a viaggiare una flotta di veicoli a guida automatica. Navette che si occupano del trasporto di materiale tra gli impianti di lavorazione e i punti di carico per la spedizione finale.
“Le navette si spostano tramite sensori per identificare il tracciato in aree dello stabilimento in cui possono incrociarsi tra di loro e aperte al transito degli operatori – commenta Emiliano Dini, responsabile Automazione dello stabilimento ravennate -. Pur dotate di tutti gli strumenti di sicurezza, è fondamentale che siano sempre connesse alla rete che ne controlla la localizzazione”.
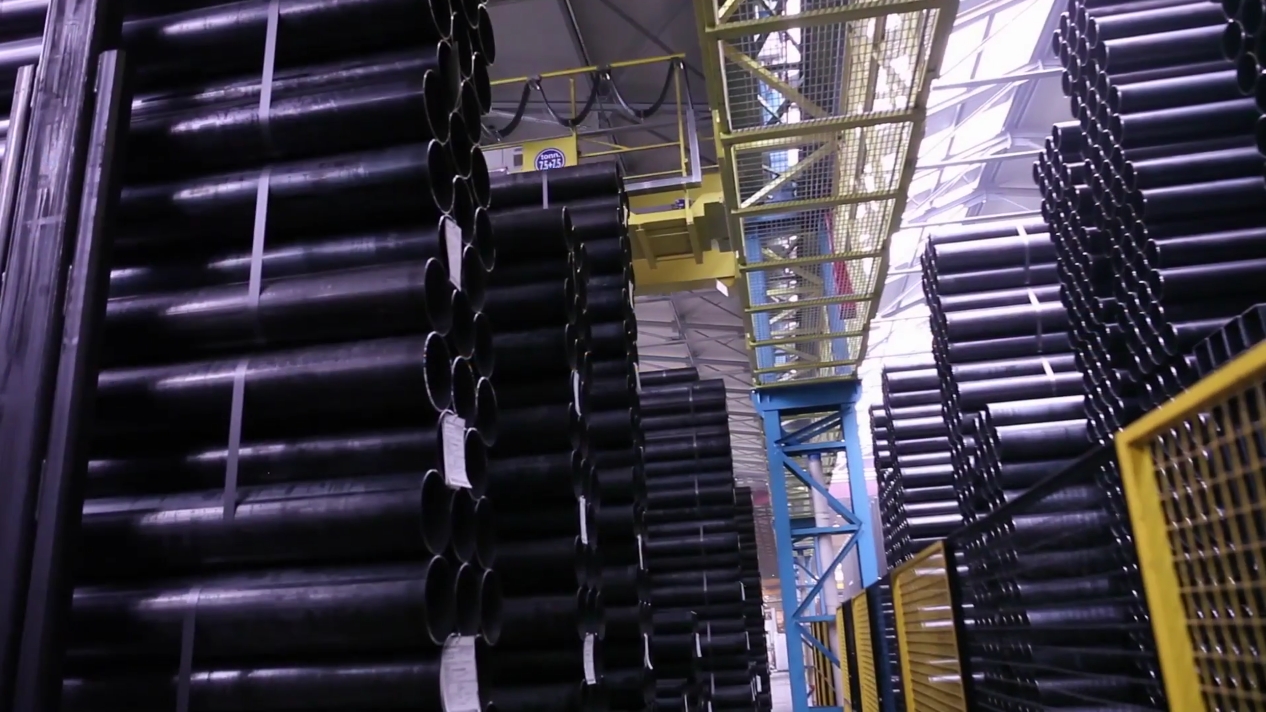
All’interno dello stabilimento di Casalmaggiore, dedicato invece alla produzione di tubature, Marcegaglia e Cisco hanno messo in piedi un sistema di carriponte intelligente e automatizzato, che effettua lo stoccaggio dei pacchi di tubi raccolti direttamente dagli impianti di produzione, movimentandoli fino all’area dove avviene il caricamento sugli automezzi di trasporto. “Anche i dati dal carroponte hanno bisogno di una trasmissione stabile e continua – spiega Roberto Ferrari, direttore dello stabilimento lombardo -. I carriponte sono impostati in modo da avere un continuo scambio in millisecondi per rilevare i rispettivi posizionamenti. Se la comunicazione non è all’altezza i carriponte rallentano e si fermano, con forti conseguenze per la produzione”.
Sia i carriponte che i mezzi AGV, attivi nei rispettivi stabilimenti, ricevono e trasmettono dati e informazioni tra di loro e con il sistema centrale che impartisce ordini e missioni e che guida le macchine con la precisione totale con cui devono muovere materiali dagli ingombri e dal peso più che consistente.
“Verso l’IoT per reingegnerizzare i processi” – L’investimento affrontato dal gruppo italiano, spiega il suo Network Infrastructure manager Livio Bonatti, “è stato operato nell’ottica di portare a termine la trasformazione di Marcegaglia in una Connected Factory, attraverso l’adozione di una rete unificata per l’azienda e gli stabilimenti, in grado di abilitare la reingegnerizzazione dei processi in ottica Internet of Things e lungo una supply chain totalmente informatizzata”.
La tecnologia e i linguaggi standard di Cisco “permettono la totale personalizzazione dei sistemi anche in ambito industriale e, di conseguenza, le prestazioni della rete”, chiarisce Bonatti che spiega come grazie all’architettura Factory Network, che permette di individuare eventuali problemi prima che si verifichino, Marcegaglia abbia ottenuto la massima visibilità su tutti gli impianti.
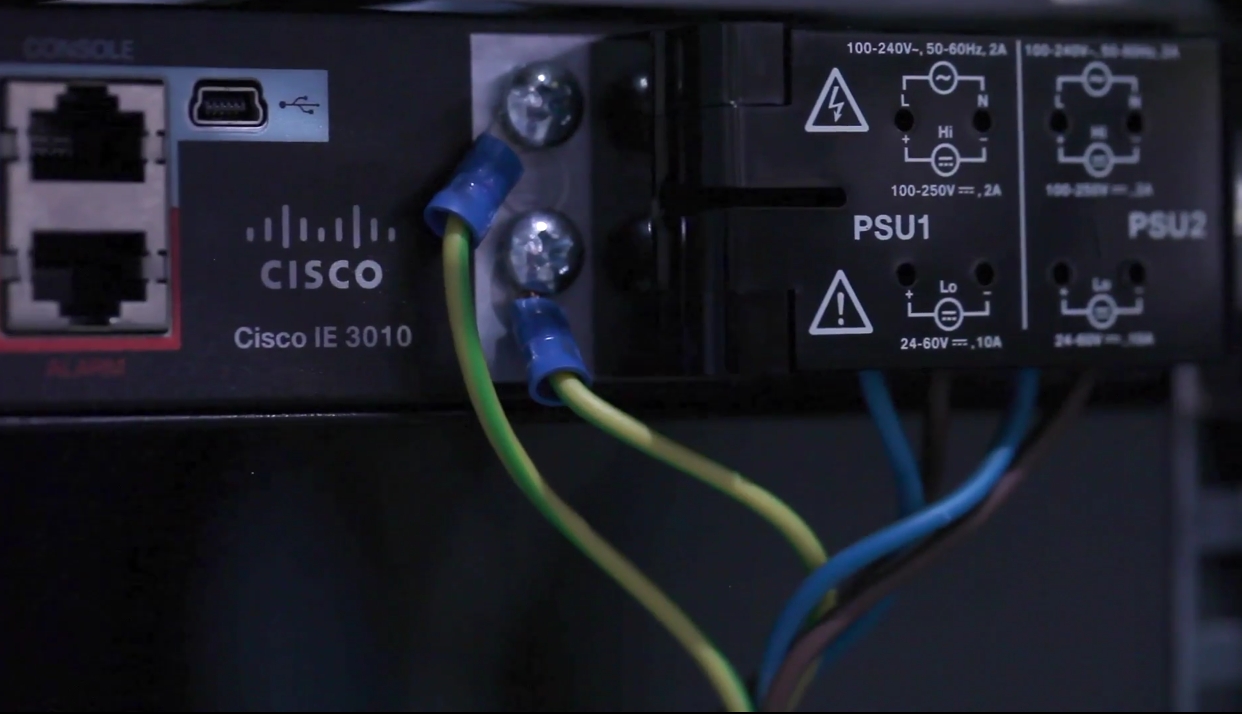
La strategia tecnologica di Marcegaglia, sottolinea Michele Dalmazzoni, Collaboration and Industry Digitization leader di Cisco Italia, “dimostra in modo evidente che dotarsi di una infrastruttura digital ready è un requisito primario per mantenere la leadership ed essere competitivi nell’era digitale”. Quando si parla di digitalizzazione, fa notare Dalmazzoni, ci si riferisce a fenomeno “che interessa tutto l’ecosistema industriale: non solo la fabbrica, in cui si realizza un’integrazione tra tecnologie IT e operative, ma anche tutta la sua supply chain e tutto ciò che riguarda i processi post- produzione, dalla distribuzione alla fornitura di servizi post vendita”.
Parole in linea con la vision del colosso californiano, che in Italia sta cercando di accelerare l’ingresso della tecnologia nelle fabbriche e più in generale di favorire lo sviluppo di un ecosistema digitale. Di questo obiettivo, il piano Digitaliani per lo sviluppo di nuove competenze 2.0, su cui Cisco sta investendo 100 milioni di dollari, ne è forse l’esempio più evidente.
Fabbrica connessa per l’industria pesante – L’architettura allestita da Marcegaglia riflette l’approccio di Cisco Factory Network. Il supporto della compagnia statunitense si è tradotto infatti non solo nella fornitura degli apparati alla base dell’infrastruttura di connettività, ma anche degli switch di fattura industriale e della componente di Factory Wireless che porta la connettività in tutti i punti dell’impianto. Come si accennava all’inizio e come dimostra anche l’ultima iniziativa lanciata da Cini, Cisco e Leonardo, ragionare di industria 4.0, industrial IoT, cloud e soci vari senza tenere a mente il tema della cybersecurity è rischiosissimo.
Non a caso, l’infrastruttura del gruppo Marcegaglia è stata completata dalla componente di Factory Security che grazie a firewall e sonde protegge la rete degli stabilimenti da attacchi esterni e interni. Il risultato, spiegano le due società, “è una piattaforma che, integrando completamente gli stabilimenti all’ambiente di rete aziendale in modo sicuro, facile da gestire e con alte prestazioni, permette tutta l’automazione degli impianti e, di conseguenza, favorisce la produttività”.
La lista dei benefici dichiarati da Marcegaglia è piuttosto importante: riduzione degli errori umani, monitoraggio degli impianti, ottimizzazione della produzione e innalzamento della sicurezza fisica e digitale. Non deve dunque stupire che leggendo le case history di chi ha già sposato il paradigma dell’industry 4.0, trovare qualcuno non soddisfatto della svolta appare davvero un’ardua impresa.
Follow @andreafrolla